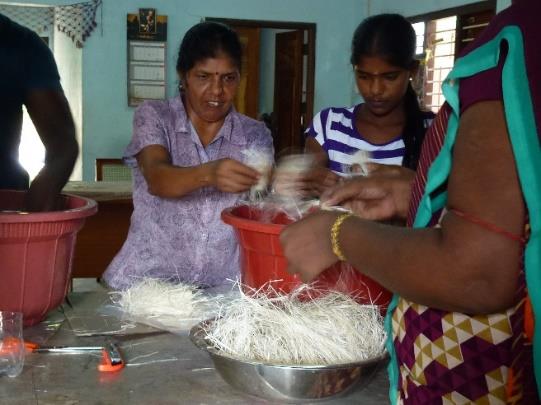
The project “Waste for Life” focused on generating poverty reducing solutions for a serious environmental issue in the country, the waste problem. This study achieved environmental sustainability by reducing the waste in the environment and, socio-economic sustainability by improving the livelihood of marginalized people in the community who work with waste.
Key aspects of this project are;
-
Current waste management system in the country and the role of the informal sector in waste management was identified.
-
Assessed the socio-economic, environmental and technical feasibility of a Waste for Life project in Sri Lanka.
-
Key stakeholders, the needs of the community and social impact of the project were identified.
-
Socio-economic and environmental sustainability of the project was found out and a small scale pilot project was implemented.
This project was an initiate in developing poverty reducing solutions through an innovative waste management approach for marginalized sectors in the community such as small scale recyclers, waste collectors and community based organizations who work on waste management.
For the past few decades the waste management in Sri Lanka has being primarily focusing on the environment. This project took a different approach and made an effort to include the marginalized sectors who work with waste into the system.
WASTE FOR LIFE AT THE UNIVERSITY OF JAFFNA, KILINOCHCHI.
I joined as a Research Assistant for this project from July 2016 to Present. My role in this project is developing a composite materials from waste plastic and natural waste (Banana fiber, fabric waste and paddy husk). And we develop some simple domestic and building materials from those materials such as notebook covers and roof sheets.
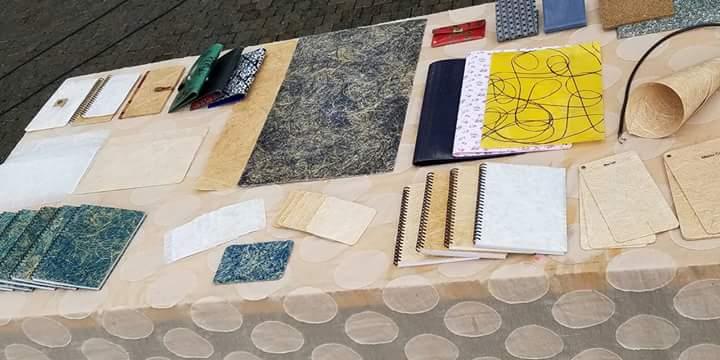
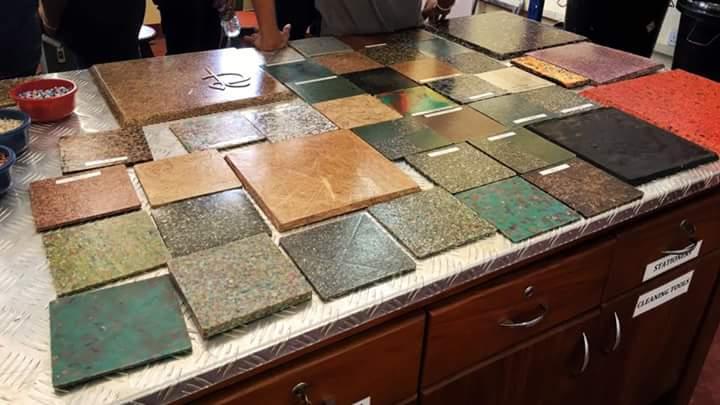
DEVELOPMENT OF A COMPOSITE MATERIAL
The composite material was developed into various steps.
First we collected the solid waste and agricultural waste from the local industries and from the farming areas. Waste material was sorted into various categories (Solid waste categorized as HDPE, LDPE etc and agricultural waste categorized as fibers, fabric waste). Then the plastic materials were mixed with the agricultural waste and fabric waste and fabric waste in various composition. Using the suitable process parameters the mixture was hot pressed. Using the shredder machine laminated material was shredded into 6 to 7 mm parts. Finally the shredded parts hot pressed to form the final composite material. To quick cool down the final composite material cold press machine was used. The process is shown in the figures below.
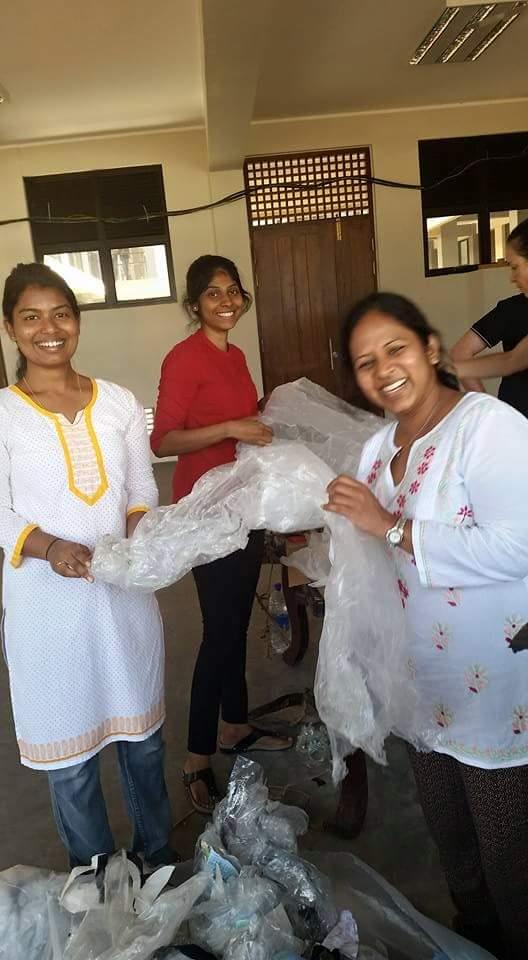
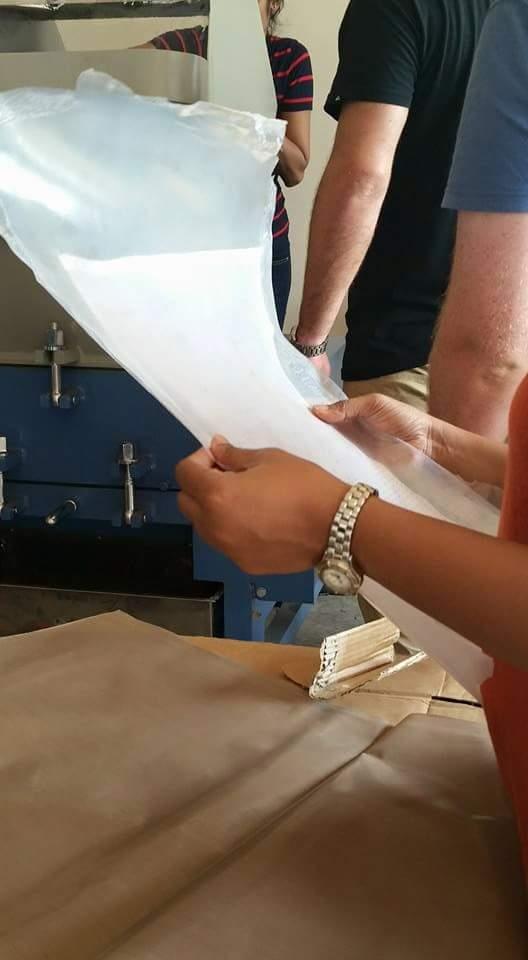
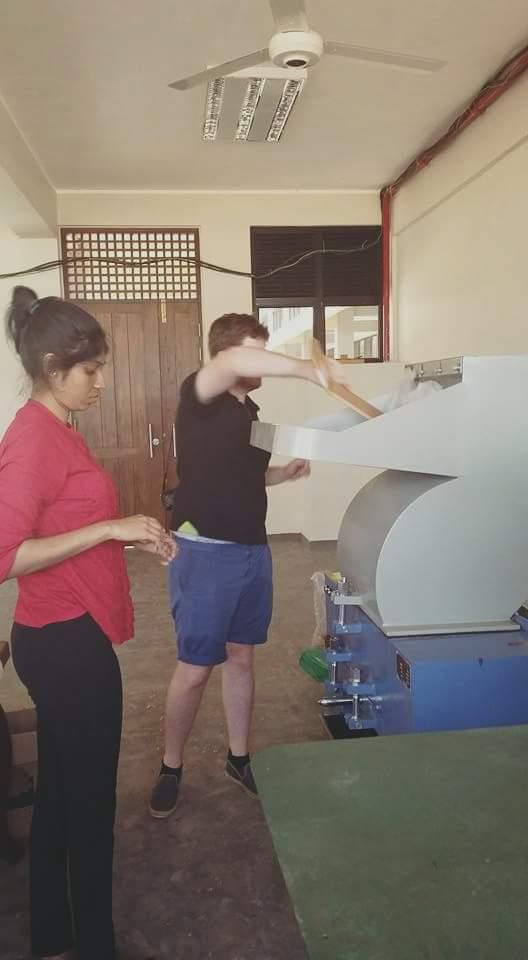
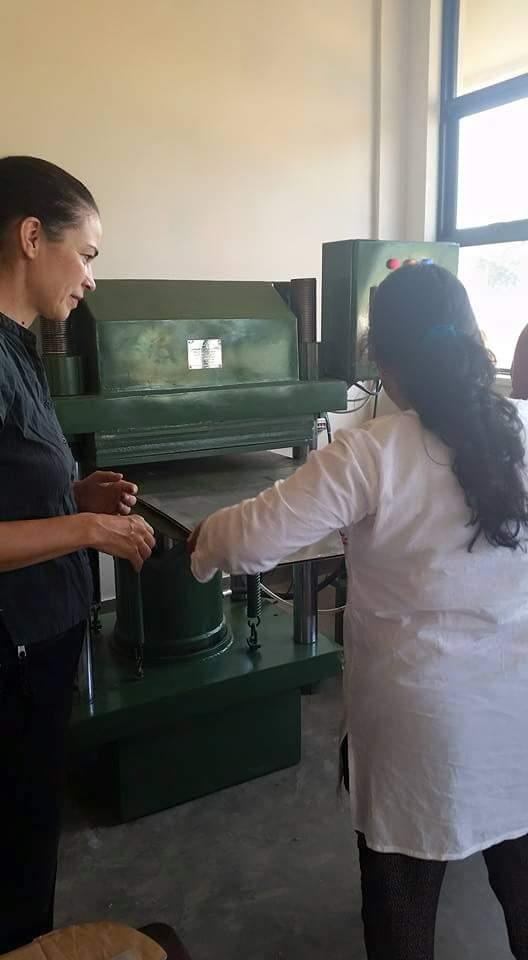
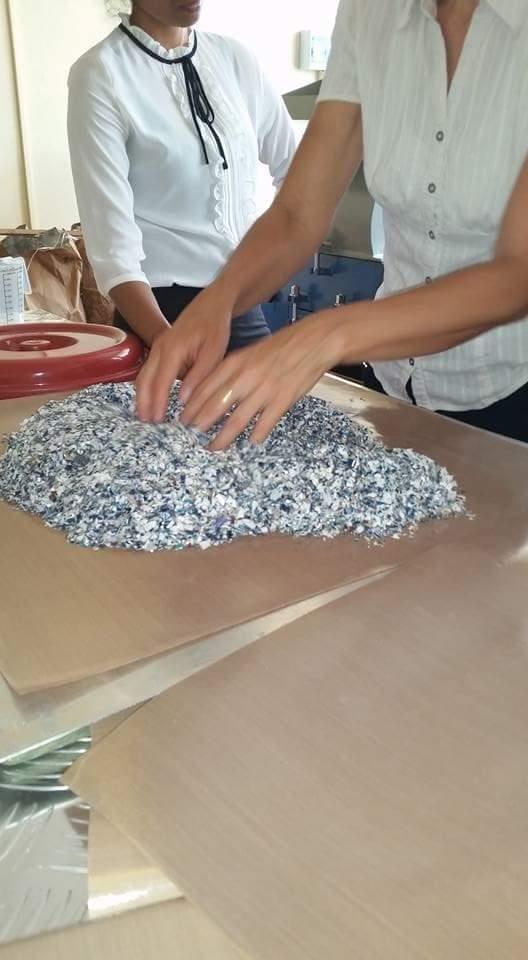
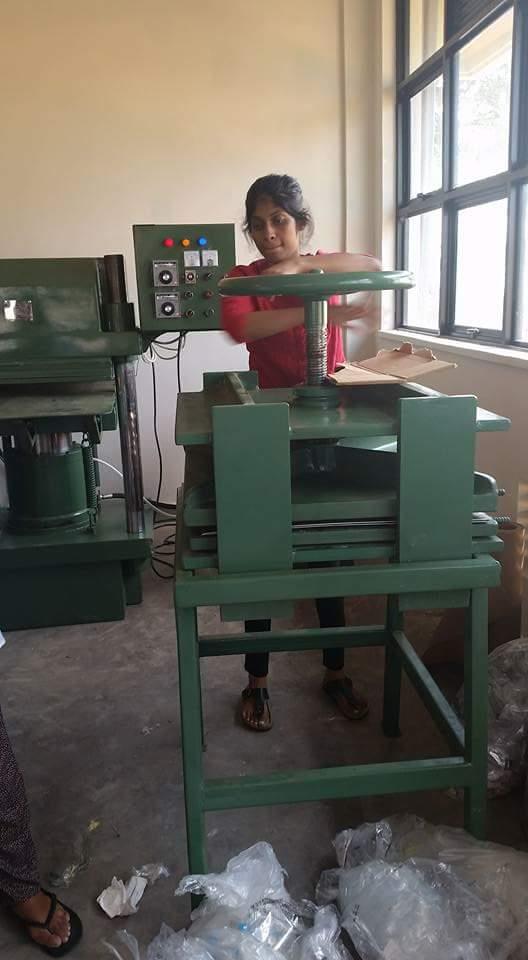
PRODUCT DESIGN
New product designs were made using the above mentioned composite materials which can be used as a substitute for materials which are currently available in the market. Some of those substituted products are shown below.
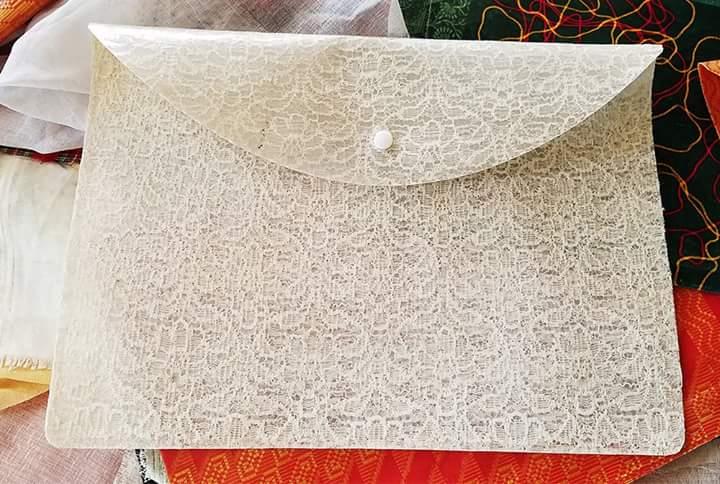
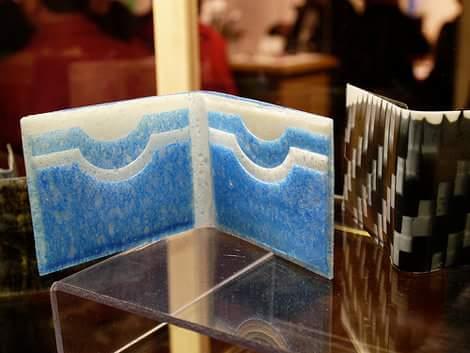

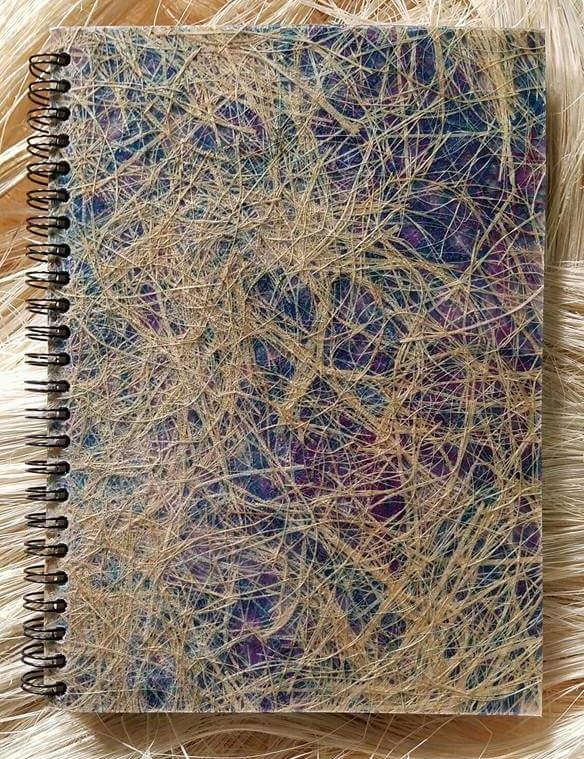
PROPER PLACE IDENTIFICATION FOR MARKETING THE PRODUCT
In order to capture the market places, our team looked into different places such as tourist places, hotels and good market etc. Possibilities were analyzed and finally the products were marketed in Kingsburry hotel, Barefoot shop.
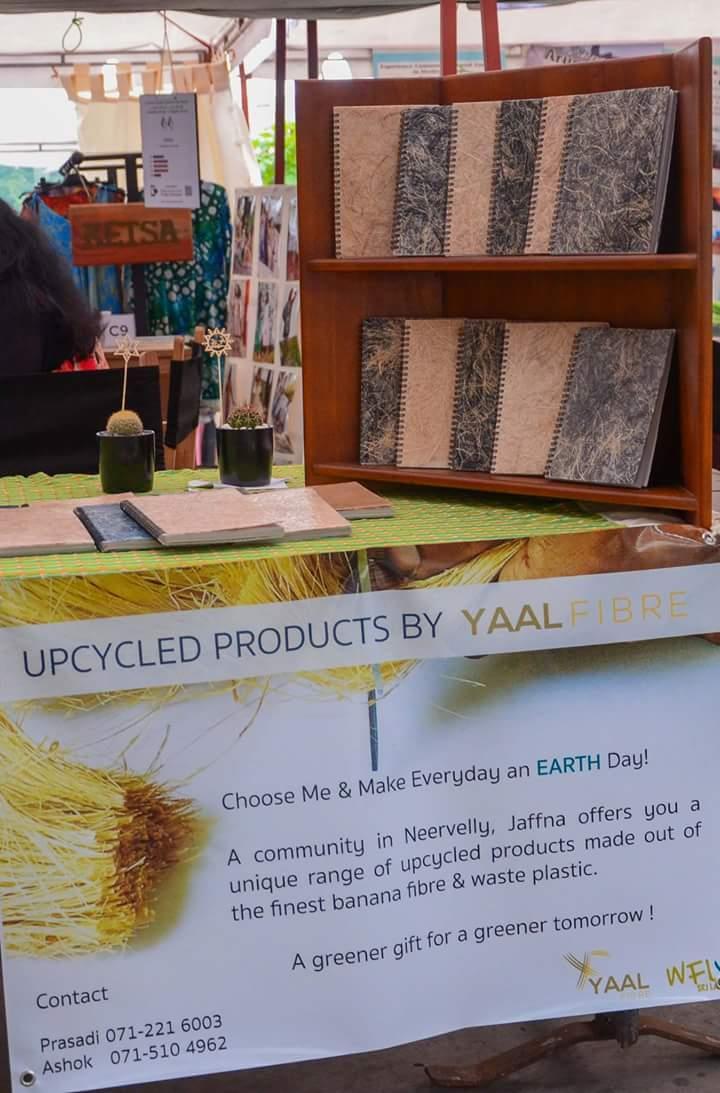
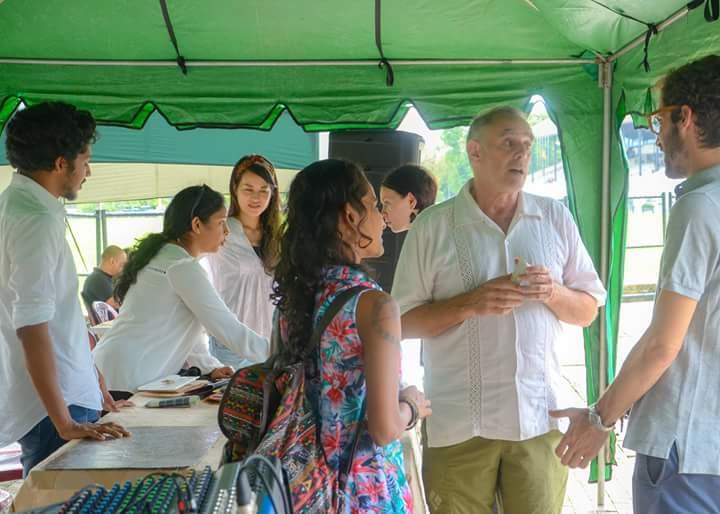
ROOF TILE DEVELOPMENT
One such material developed was WFL roof tile for toilet, which is an alternative for the traditional asbestos roof. The process of making the WFL roof and fixing was shown below.
The tiles were made by combining two different types of agricultural waste, with waste HDPE plastic obtained from industry sides around Jaffna. The Rice Husk tiles are composed of 10% RIce Husk ans 90% HDPE by weight. (Different combinations of agricultural and Solid waste were tried to find out the ideal composition to make the tiles.) The RIce Husk was obtained from a wholesale rice supplier from a shop in Jaffna. The Banana Fibre tiles on the other hand were made from shredding the offcuts of the sheets used to make Yaal Fibre products such as the books, placements and coasters. 15% Banana Fibre and 85% HDPE by weight was used to make tiles. This is the first application of our prototype asbestos replacement project, which substitute upcycled fiber reinforced waste plastics for traditional asbestos roofs. Waste for Life is now conducting tests at The University of Western Australia and The Industrial Technology Institute of Sri Lanka.
The step after manufacturing the tiles is to purchase the timber required. One of the apparent reasons for the tendency to use asbestos roofing despite the obvious risks is the size of the asbestos sheets is timber. Commercial asbestos sheets come in sizes of 6×3 ft2 upwards to 12×3 ft2. Consequently the amount of timber required for fixing sheets of this size is much smaller, thereby reducing the overall cost as timber relatively expensive. For the construction of our toilet block roof, we needed 2 principal beams and 6 transverse battens which cost 3500LKR. It should be noted that prior to the this, there were only 2 principal beams used and no transverse battens to affix the asbestos sheet which would have costed 700LKR. This required vertical slots to be grinded into the blockwork for the principal beams to be slotted into, in the manner of the picture below.
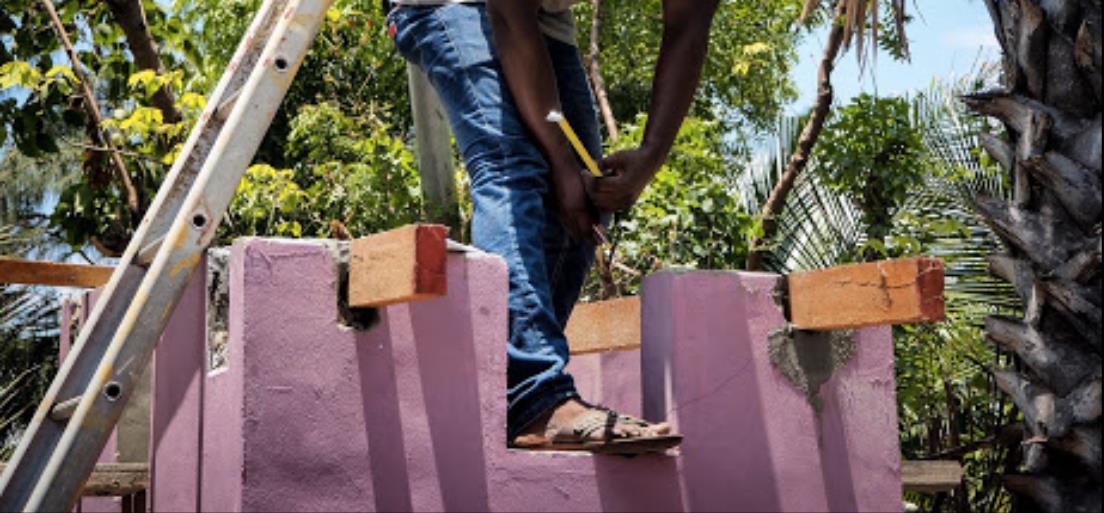
The sketch below outlines the design of the roof constructed at Irupalai.
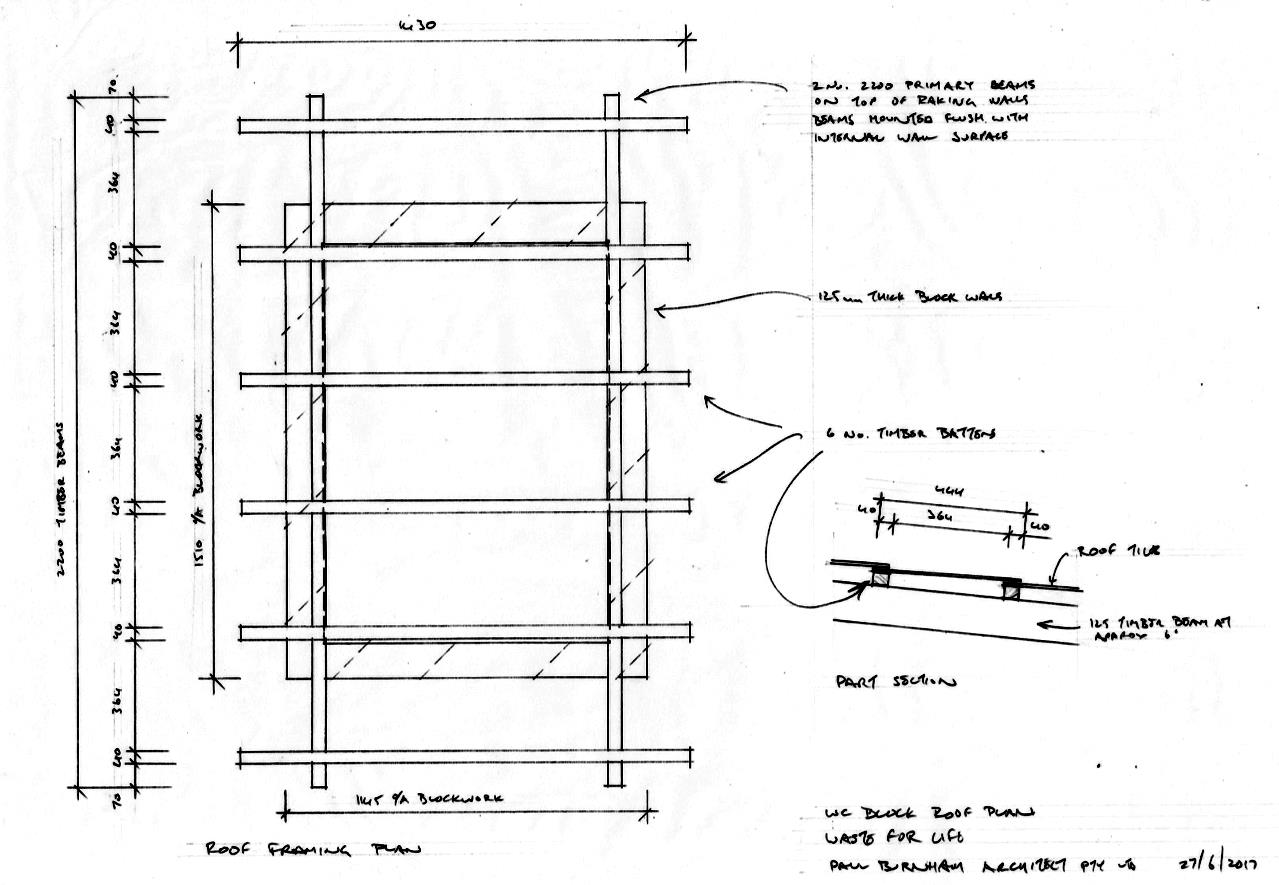
Next, the transverse battens and tiles were drilled into the principal beams. Following a suggestion from Chern Ng, to help the waterproofing nature of the roof, the tiles were laid in the below formation in the transverse direction.
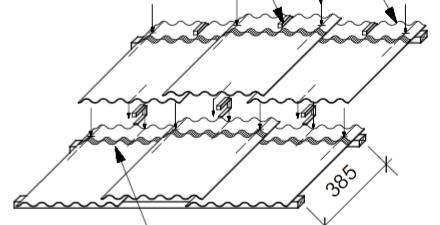
The last thing to note is that, for aesthetic reasons, we chose to do alternate rows of Rice Husk and Banana Fibre tiles, which by no means is vital to the properties of the roof. The picture below shows the completed roof that laid on the toilet for a house in Irupalai.
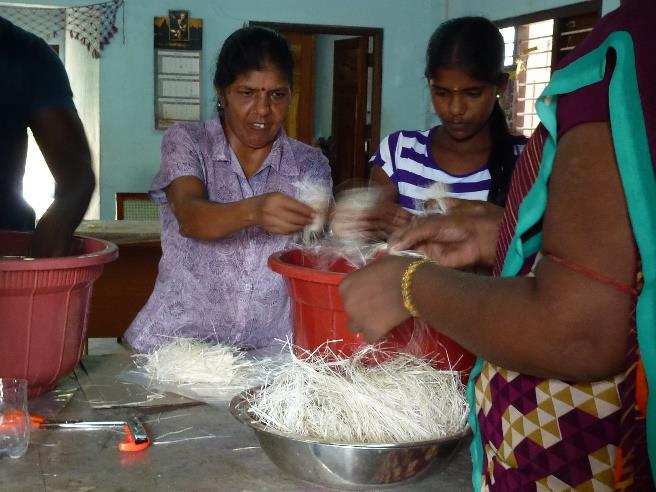
COMMUNITY WORK
More that a single person work, this project is a team work which includes Project Manager, Designers from various countries, Research Assistants, Community coordinators. Once the material is designed by Research Assistant, products are designed by the designers and final products are marketed by the Community coordinators. Local communities who were already dealing with the waste recycles are identified and the knowledge required to do this work, training were given to those local communities freely. Profit by selling those products is gained fully by those local communities.
Workshop in Neerveli Banana Cooperative, Jaffna.
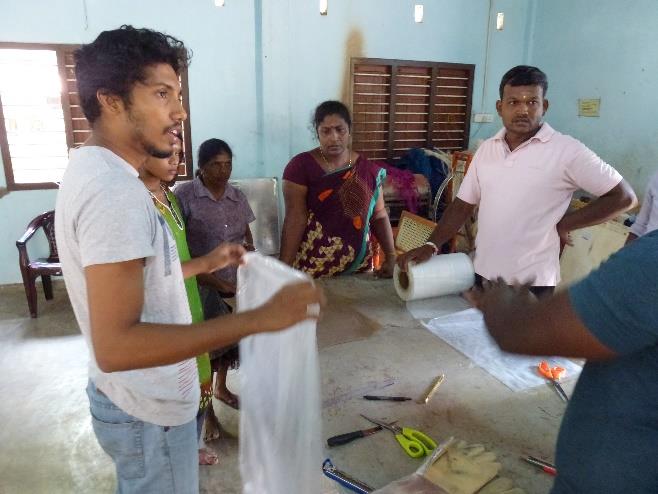
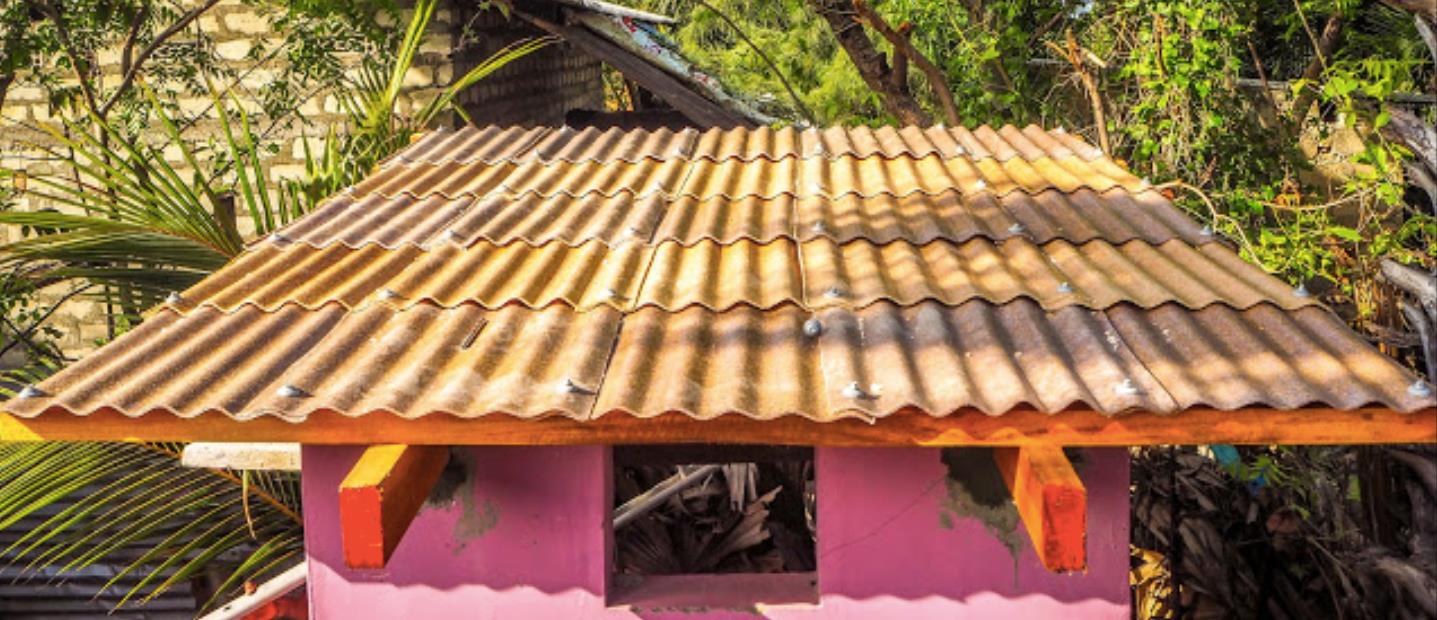
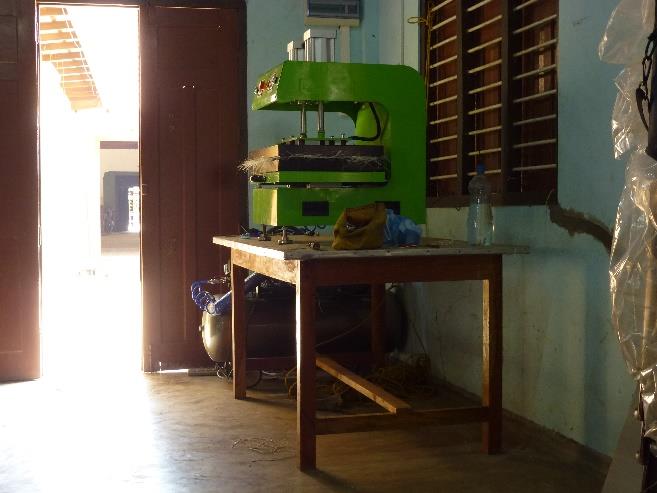
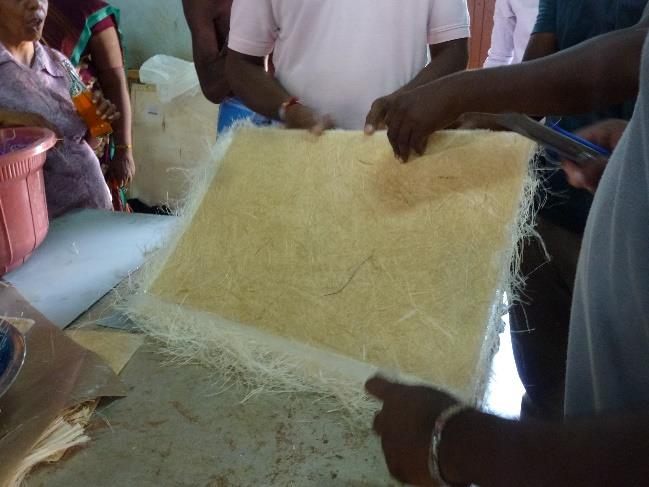
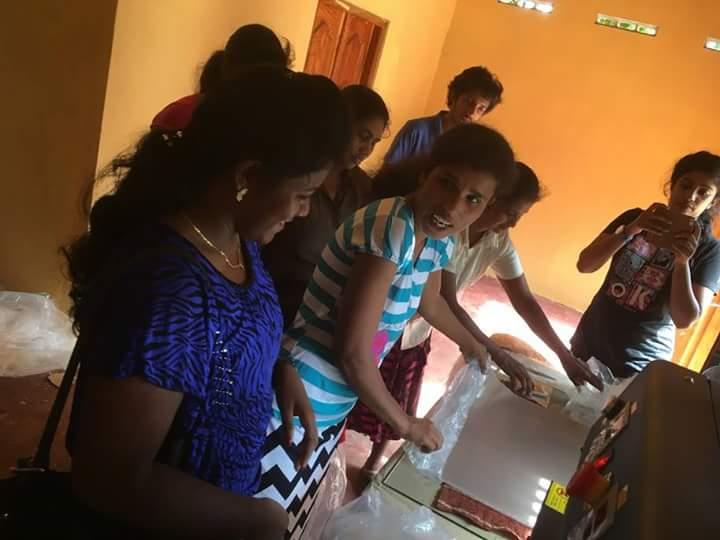
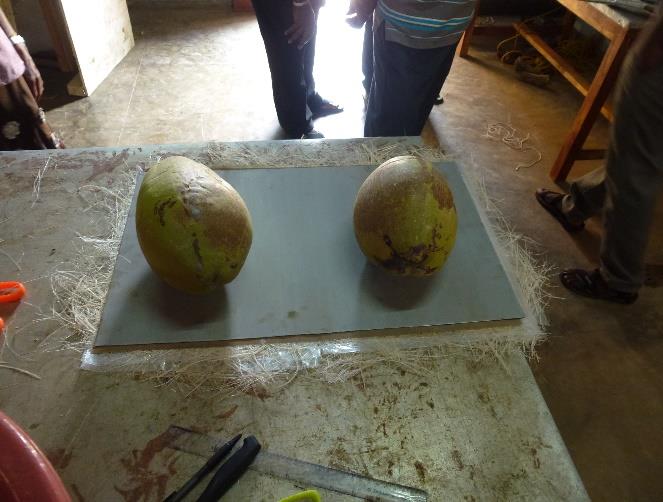
Workshop in Irupalai Palam Community Jaffna.
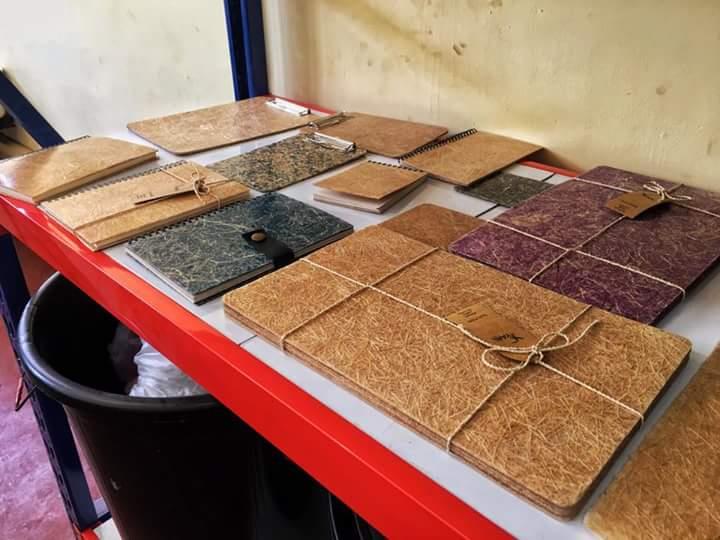
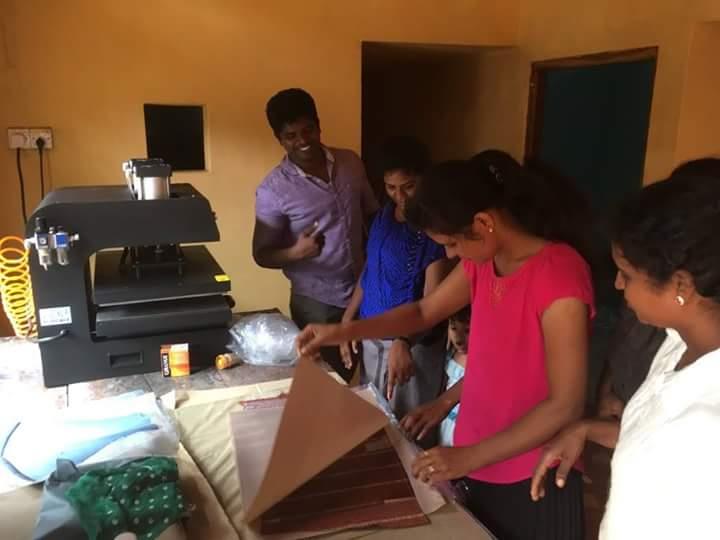
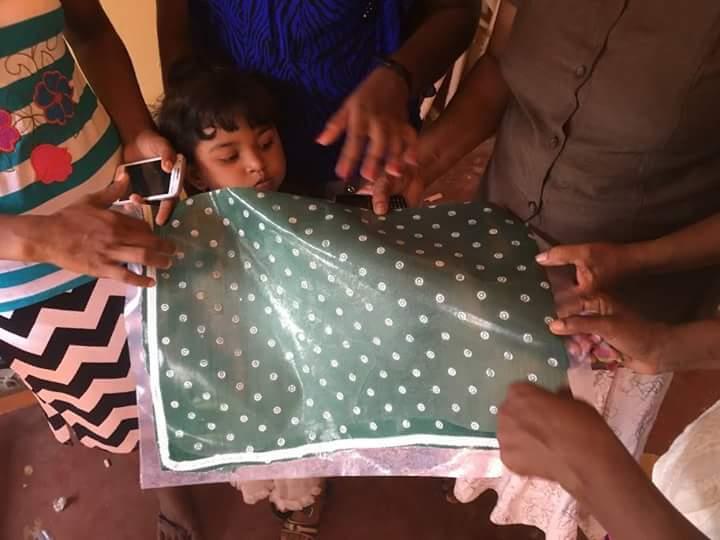
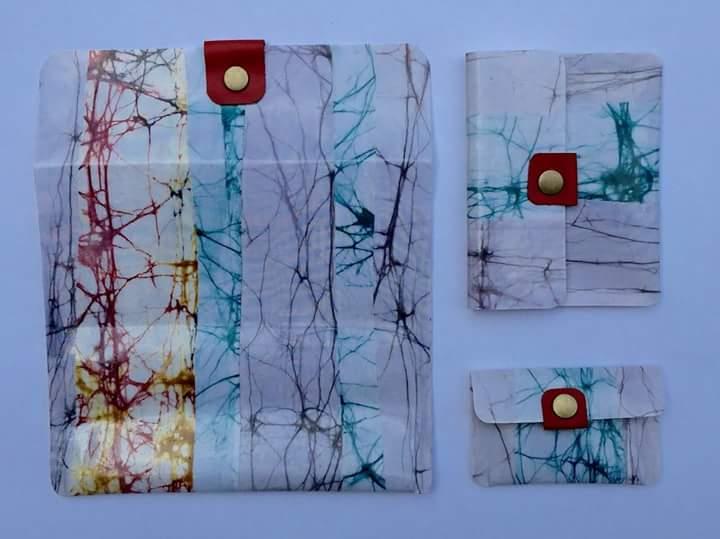
This is one of the significant project which uplifts the livelihood of the marginalized people in all over the part of Sri Lanka. More than that waste production is one of the uprising crisis all over the world. Plastic is one of the important waste generated all over the part of Sri Lanka. Thorugh this project both the natural waste as well as the artificial wastes like plastic can be reduced and they become as a commercial valued products. Sri Lanka is one of the growing country in the world, improving the livelihood of the people is one of the vital need and the people who are affected by the war can too improve their livelihood through this project. The funding for the money is to be finished in this December 2017. Taking over this project will be benefit the livelihood of the people and enhance the environmental effects.